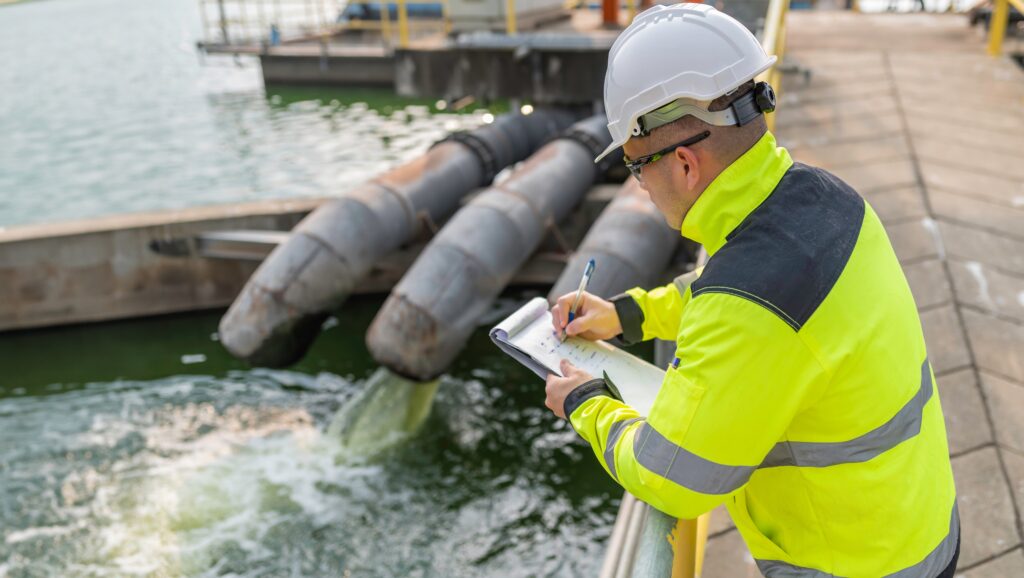
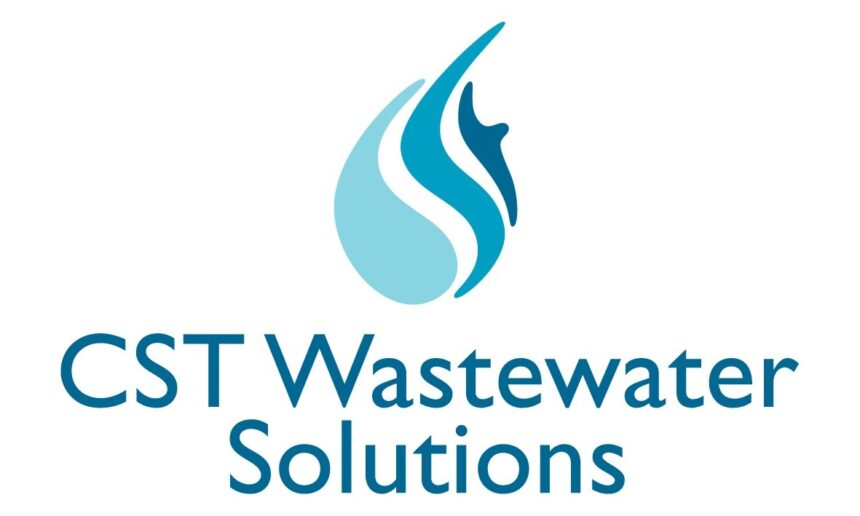
A company with 35 years of experience in municipal and industrial wastewater technology in Australia and New Zealand says users of wastewater plants should inspect inlet screening as a priority to safeguard against emerging new challenges affecting performance.
CST Wastewater Solutions’ Managing Director Michael Bambridge says screens are the first line of defence in both industrial and municipal water and wastewater treatment, where they get the dirtiest and most testing primary inlet jobs that can degrade their performance and potentially lead to environmental spills.
“But, on the positive side, good pre-screening processes also present the first opportunity in the wastewater treatment process chain for users to safeguard against challenges presented by climate change and ingestion of plastic waste and other environmental challenges that can lead to blockages and spillages,” says Michael.
His company – which conducts inspections of screens to ensure they are complying with OEM performance standards or better – is a national leader in introducing new technologies such as ultra-fine screening down to .02mm mesh designed to stop problems before they start.
“In the course of our inspection work, we are also finding big problems arising with some imported wastewater treatment plants brought on up-front price alone. This simply transfers the true cost of good wastewater treatment further down the timeline – when it is more expensive to fix and more likely to fail suddenly, with potential process interruptions and environmental spills.
“For example, we recently had to totally replace, after just five years’ service, a rusted-out, poorly protected steel set of screens for a municipality servicing tens and thousands of people and businesses. These were replaced with locally manufactured fit-for-purpose stainless steel screens that typically last at least three times longer and do a finer screening job.”
Why Australian-manufactured screens deliver long term ROI
Investment in poorly made screens is made even worse in those cases where they may have very slow or non-existent service from somewhere overseas when things go wrong, says Michael, who is a chemical engineer overseeing wastewater and recycling projects that have won local and international acclaim, including Highly Commended for a waste-to-energy project from the chemical engineering peak group IChemE (Institution of Chemical Engineers) with 30,000 members in 114 countries.
CST has moved to local production of its robust stainless steel pre-screening technologies to ensure top Australasian standards of engineering and performance in changing conditions, including increasingly variable flow rates as a result of climate change. It has also introduced some of the world’s finest pre-screening to stop plastics and some microplastics, down to .02mm, entering the waste stream of process and recycling plants, potentially damaging them or causing environmental spills.
It has complemented its availability of on-site service for WWTPs in Australia and New Zealand with dedicated screen inspection services to determine performance levels and best suitability for local conditions in the areas involved.
“Wastewater treatment – both municipal and industrial – can never be one-size-fits-all, which it may be in the case of imported standards solution designed on the other side of the world for conditions there.
“Apart from taking local jobs, deficient product can be a cheap and short-sighted approach that comes undone the first time something goes wrong. Often the organisation using it doesn’t have the specialist engineering resources to fix it (which is the case with many smaller and mid-sized municipalities and industrial users, including some food and beverage and primary production organisations).”
Why check wastewater screens?
Michael says inlet screens can look pretty good to the untrained eye, so the temptation may always be there to check and forget, to save a few dollars if there is no obvious problem. This set-and-forget approach can become a costly lesson for multiple reasons, including risk management and a Duty of Care to safeguard against OH&S issues that can reasonably be foreseen as arising arise when handling waste spillages, and the Statutory environmental implications of such spills.
“Most companies these days are pretty risk aware. They know production stoppages are costly, and environmental spills can affect their statutory licence to operate. But we still do see poorly maintained plants causing issues for the operator, reasonably often. These should be a thing of the past, when small investment in yearly maintenance and check-ups can return good value and ROI throughout the long term.”
About us:
Contact details:
Jack Mallen-Cooper
PR Consultant
Whyte Public Relations
(02) 9901 4306
whytepr@whytepr.com.au